Wirtschaftlichkeit der Kohlenstoffabscheidung verbessert
Forscher der Northwestern University in Evanston/Illinois haben in Zusammenarbeit mit einem internationalen Team Essigsäure aus Kohlenmonoxid (CO) hergestellt, das aus abgeschiedenem Kohlenstoff stammt. Die Innovation, bei der ein neuartiger, im Labor von Professor Ted Sargent entwickelter Katalysator zum Einsatz kommt, könnte das Interesse an der Kohlenstoffabscheidung und -speicherung neu beflügeln. Die Arbeit wurde am 03.05.2023 in Nature veröffentlicht.
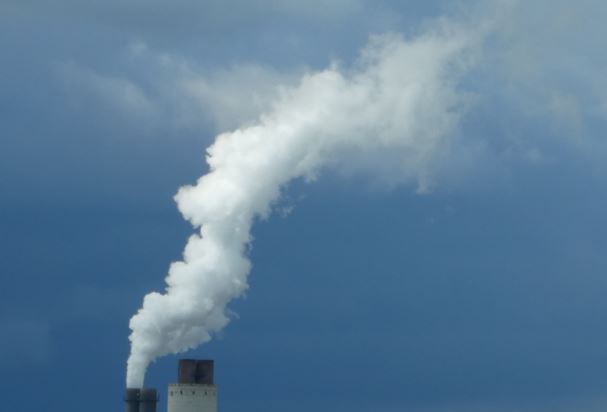
CO2, Wasserdampf und Rauch aus Kraftwerk in Berlin – Foto © Gerhard Hofmann, Agentur Zukunft, für Solarify
„Die Kohlenstoffabscheidung ist heute technisch machbar, aber noch nicht wirtschaftlich“, so Forschungsleiter Ted Sargent. „Indem wir die Elektrochemie nutzen, um abgeschiedenen Kohlenstoff in Produkte mit etablierten Märkten umzuwandeln, bieten wir neue Wege zur Verbesserung dieser Wirtschaftlichkeit sowie eine nachhaltigere Quelle für die Industriechemikalien, die wir immer noch benötigen.“
27 Mio. Tonnen weniger Essig
Das Einsparpotenzial liegt laut Sargent bei 27 Mio. Tonnen pro Jahr – ohne Haushaltsessig, der mache allerdings nur drei Prozent der Gesamtmenge aus. Auch wenn Essigsäure vor allem als Hauptbestandteil von Haushaltsessig bekannt ist, sagt Josh Wicks, dass diese Verwendung nur einen kleinen Teil ihrer Einsatzmöglichkeiten ausmacht: „Essigsäure in Essig muss aus biologischen Quellen durch Gärung gewonnen werden, da sie vom Menschen konsumiert wird“, so Wicks. „Aber etwa 90 % des Essigsäuremarktes sind Ausgangsstoffe für die Herstellung von Farben, Beschichtungen, Klebstoffen und anderen Produkten. Die Produktion in diesem Umfang erfolgt hauptsächlich aus Methanol, das aus fossilen Brennstoffen gewonnen wird.
Datenbanken zur Ökobilanzierung zeigten dem Team, dass für jedes Kilogramm Essigsäure, das aus Methanol hergestellt wird, 1,6 kg CO2 freigesetzt werden. Ihre alternative Methode erfolgt in einem zweistufigen Prozess: Zunächst wird das abgeschiedene gasförmige CO2 durch einen Elektrolyseur geleitet, wo es mit Wasser und Elektronen zu CO reagiert. Das gasförmige CO wird dann durch einen zweiten Elektrolyseur geleitet, wo ein weiterer Katalysator es in verschiedene Moleküle mit zwei oder mehr Kohlenstoffatomen umwandelt.
„Eine große Herausforderung für uns ist die Selektivität“, so Wicks. „Die meisten Katalysatoren, die für diesen zweiten Schritt verwendet werden, ermöglichen mehrere gleichzeitige Reaktionen, was zu einer Mischung aus verschiedenen Zweikohlenstoffprodukten führt, die schwer zu trennen und zu reinigen sein können. Wir haben hier versucht, Bedingungen zu schaffen, die ein Produkt vor allen anderen begünstigen.“
Vinayak Dravid, Gründungsdirektor des Northwestern University Atomic and Nanoscale Characterization (NUANCE) Center, das dem Team den Zugang zu verschiedenen Möglichkeiten für Messungen von Materialien auf atomarer und elektronischer Ebene ermöglicht: „Moderne Forschungsprobleme sind komplex und vielschichtig und erfordern vielfältige und dennoch integrierte Fähigkeiten zur Analyse von Materialien bis hinunter auf die atomare Skala. Kollegen wie Ted stellen uns vor herausfordernde Probleme, die unsere Kreativität anregen, neue Ideen und innovative Charakterisierungsmethoden zu entwickeln“.
Die Analyse des Teams zeigte, dass die Verwendung eines viel geringeren Kupferanteils (etwa 1 %) im Vergleich zu früheren Katalysatoren die Produktion von reiner Essigsäure begünstigt. Außerdem zeigte sich, dass eine Erhöhung des Drucks auf 10 Atmosphären dem Team eine rekordverdächtige Effizienz ermöglichen würde.
In dem Papier berichtet das Team über einen faradayschen Wirkungsgrad von 91 %, was bedeutet, dass 91 von 100 in den Elektrolyseur gepumpten Elektronen im gewünschten Produkt – in diesem Fall Essigsäure – landen. „Das ist die höchste Faraday-Effizienz für ein Multi-Kohlenstoff-Produkt bei einer skalierbaren Stromdichte, die uns bekannt ist“, so Wicks. „Katalysatoren, die auf Ethylen abzielen, erreichen in der Regel eine maximale Effizienz von 70 bis 80 %, wir liegen deutlich darüber“.
Der neue Katalysator scheint auch relativ stabil zu sein: Während die Faraday-Effizienz mancher Katalysatoren im Laufe der Zeit abnimmt, konnte das Team zeigen, dass sie selbst nach 820 Betriebsstunden auf einem hohen Niveau von 85 % blieb. Wicks hofft, dass die Elemente, die zum Erfolg des Teams führten – darunter ein neuartiges Zielprodukt, ein leicht erhöhter Reaktionsdruck und ein geringerer Kupferanteil im Katalysator – andere Teams dazu inspirieren, über den Tellerrand hinauszuschauen.
->Quellen: