Neues Niedrig-PH-System recycelt mehr Kohlenstoff in wertvolle Produkte
Forscher der Fakultät für Ingenieurwesen an der Universität Toronto („U of T Engineering“) haben ein verbessertes elektrochemisches System entwickelt, das den Einsatz von abgeschiedenem CO2 aufwertet, indem es mehr davon in wertvolle Produkte umwandelt als je zuvor, schreibt Tyler Irving am 03.06.2021 auf der U of T Engineering News-Seite. Die IEA hat CCS und CCU zwar für geeignet gehalten, um die globale Erwärmung bis 2050 auf 1,5 C zu begrenzen. Doch die Abscheidung von Kohlenstoff hat derzeit kaum wirtschaftlichen Wert; das verringert den Anreiz für Unternehmen, in diese Technologie zu investieren.
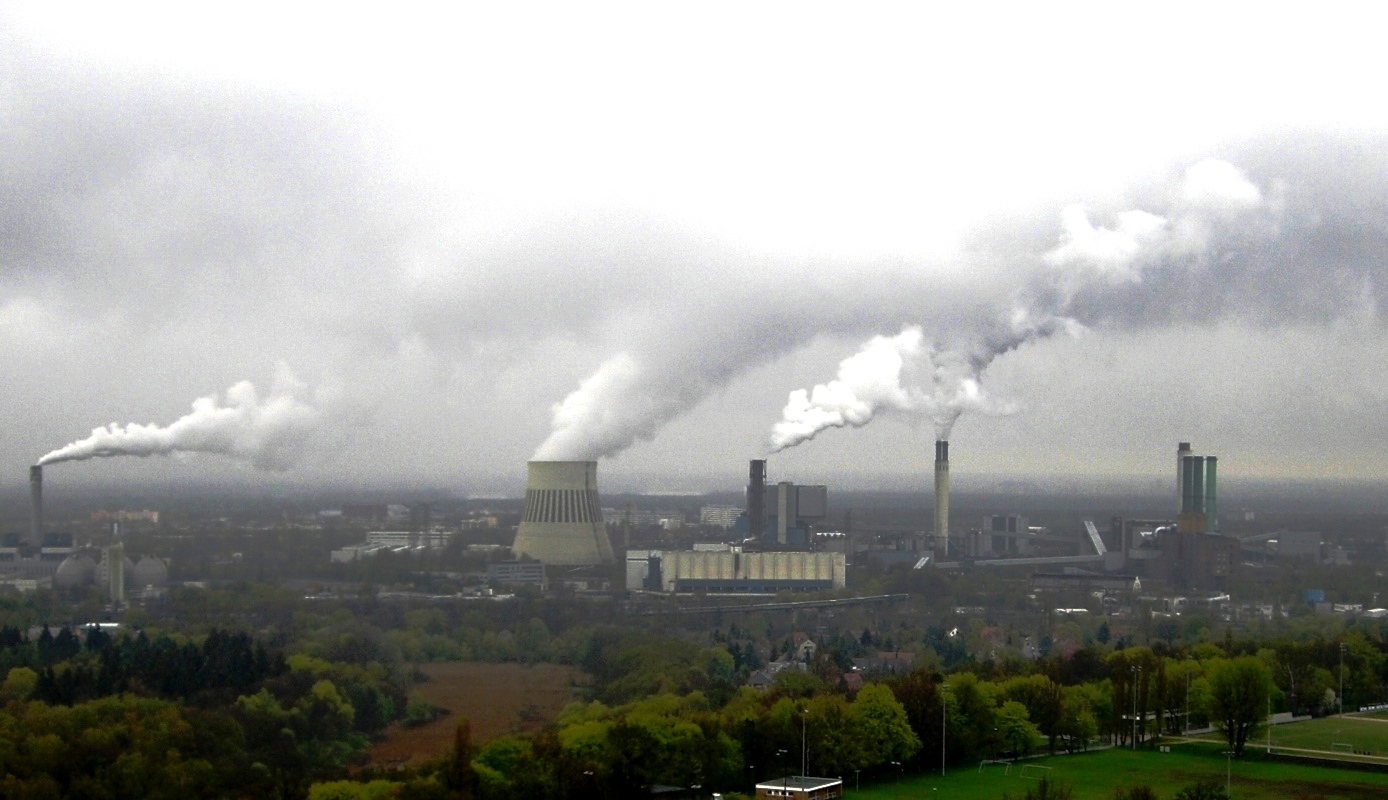
CO2, Wasserdampf und Rauch – Kraftwerke im Nordwesten Berlins – Foto © Gerhard Hofmann für Solarify
Ein Team der U of T Engineering unter Leitung von Professor Ted Sargent geht dieses Problem an, indem es fortschrittliche Elektrolyseure entwickelt, die abgeschiedenes CO2 in die petrochemischen Bausteine gängiger Alltagsmaterialien zerlegen, von Plastik bis Lycra (Elastan). Dies trägt dazu bei, einen Markt für abgeschiedenen Kohlenstoff zu schaffen, und bietet gleichzeitig eine kohlenstoffarme Alternative zu den heute verwendeten, auf fossilen Brennstoffen basierenden Herstellungsprozessen.
Im Gegensatz zu früheren Systemen kann das neueste Design des Teams unter stark sauren Bedingungen betrieben werden, was unerwünschte Nebenreaktionen reduziert und die Gesamteffizienz erhöht. „Bei früheren Systemen musste man sich entscheiden, ob man sich auf die effiziente Nutzung von Elektrizität oder auf die effiziente Nutzung von Kohlenstoff konzentrieren wollte“, sagt Sargent, Hauptautor der am 03.06.2021 in Science veröffentlichten neuen Untersuchung. „Unser Team hat ein neues Katalysatordesign innerhalb des Elektrolyseurs verwendet, um einen großen Teil des zugeführten Kohlenstoffs zu verbrauchen und gleichzeitig eine gute Produktivität für die gewünschten hochwertigen Produkte zu erhalten.“
Im Elektrolyseur wird das abgeschiedene CO2 in einem flüssigen Elektrolyten gelöst, der über den festen Katalysator fließt, durch den die Elektrizität zugeführt wird. „Was wir wollen, ist, dass das gelöste CO2 im Reaktor Elektronen absorbiert und in Ethylen und andere Produkte umgewandelt wird“, sagt ECE-Doktorand Jianan Erick Huang, einer der drei Co-Lead-Autoren der neuen Arbeit zusammen mit seinem ECE-Doktorandenkollegen Adnan Ozden und dem Postdoktoranden Fengwang Li, der jetzt ähnliche Forschungen an der Universität Sydney fortsetzt. „Aber in früheren Berichten, die bei hohen pH-Werten – also alkalischen oder neutralen Bedingungen – arbeiteten, wurde der größte Teil des CO2 verschwendet, weil es stattdessen in Karbonat umgewandelt wurde.“
Huang sagt, das Karbonat könne zwar extrahiert, in CO2 umgewandelt und wieder in den Elektrolyseur eingespeist werden, das sei aber energetisch sehr aufwändig. Die Berechnungen des Teams zeigen, dass auf diese Weise mehr als die Hälfte der Energie, die das Gesamtsystem verbraucht, für das Recycling des Karbonats aufgewandt würde. Der Betrieb des Elektrolyseurs bei niedrigem pH-Wert, also unter sauren Bedingungen, verhindert zwar die Bildung von Karbonat, bringt aber ein anderes Problem mit sich: Jetzt ist die günstigere Reaktion die Wasserstoffentwicklung. Das bedeutet, dass Wasserstoffionen (d. h. Protonen) in der sauren Lösung Elektronen absorbieren und in Wasserstoffgas umgewandelt werden, so dass nur wenige Elektronen für die Verbindung mit CO2 zur Verfügung stehen.
Huang und das Team begegneten diesem Problem mit zwei kombinierten Strategien:
- Erstens erhöhten sie unter sauren Bedingungen die Stromdichte und überfluteten den Reaktor mit Elektronen. Wasserstoffionen stürmten hinein, um mit ihnen zu reagieren, aber sie blieben in einem molekularen Stau stecken – der Fachbegriff lautet Massentransportlimitierung. „Im Endeffekt schaffen wir einen Reaktor, der durchgängig sauer ist, mit Ausnahme einer winzigen Schicht innerhalb von weniger als 50 Mikrometern an der Katalysatoroberfläche“, sagt Huang. „In diesem speziellen Bereich ist er nicht sauer, sondern sogar leicht alkalisch. Dort kann das CO2 durch diese Elektronen zu Ethylen reduziert werden.“
- Der nächste Schritt bestand darin, ein positiv geladenes Ion, in diesem Fall Kalium, in die Reaktion einzubringen. Dies erzeugte ein elektrisches Feld in der Nähe des Katalysators, das es dem CO2 erleichterte, an der Oberfläche zu adsorbieren, was ihm einen Vorteil im Wettbewerb mit dem Wasserstoff verschaffte.
Diese beiden Änderungen verursachten einen großen Unterschied: Frühere Systeme nutzten in der Regel weniger als 15 % des verfügbaren Kohlenstoffs und verloren den Rest an Karbonat. Das neue System nutzt etwa 77 % des verfügbaren Kohlenstoffs, wobei mehr als 50 % in Multi-Kohlenstoff-Produkte wie Ethylen und Ethanol umgewandelt werden. (Die anderen 27 % werden zu Ein-Kohlenstoff-Produkten wie Kohlenmonoxid und Ameisensäure umgewandelt).
„Dieser Durchbruch ebnet den Weg in eine wirtschaftlich tragfähige Zukunft für die CO2-Nutzung, auch wenn die Kosten für die CO2-Abscheidung heute noch hoch sind“, sagt Philip Llewellyn, CCU-Manager bei der TOTAL SE, welche die Forschung finanziell unterstützt hat. „Wenn man darüber hinaus die prognostizierten Erhöhungen der Kohlenstoffsteuer berücksichtigt, die notwendig sind, um die globalen Klimaziele zu erreichen, bedeutet dies eine signifikante Beschleunigung der Zeit bis zur Markteinführung und der Auswirkungen auf das Klima für CO2-Elektrolyseure.“ Und Maximilian Fleischer, Chief Key Expert bei der Siemens Energy Global GmbH: „Mit der Dekarbonisierung unserer Volkswirtschaften ist die Erzeugung von Kohlenwasserstoffen aus CO2 und erneuerbaren Energien ein unbestrittenes Muss für die Speicherung von Energie und die Bereitstellung von chemischen Rohstoffen. „Die attraktive direkte elektrochemische CO2-Route litt bisher unter der geringen Ausnutzung des CO2, daher ist dieser wissenschaftliche Durchbruch, der mehr als drei Viertel der CO2-Ausnutzung in einem Durchgang ermöglicht, von entscheidendem strategischen Wert für die Industrialisierung in Richtung einer beschleunigten Klimawirkung.“
Es gibt noch Hürden zu überwinden, bevor dieses System auf ein industrielles Niveau skaliert werden kann, einschließlich der Stabilität des Katalysators, wenn er vergrößert wird, und der Notwendigkeit für weitere Energieeinsparungen. Dennoch ist Huang stolz auf das, was das Team erreicht hat: „Indem wir einen Reaktor geschaffen haben, der an einer Stelle sauer und an einer anderen Stelle alkalisch ist, haben wir eine theoretische Grenze durchbrochen“, sagt er. „Wir müssen nicht zwischen Kohlenstoff- und Elektroneneffizienz wählen: Wir können beides optimieren, um das beste Gesamtsystem zu erhalten. Es wird eine Herausforderung sein, aber ich denke, jetzt ist es machbar.“
->Quellen: