Neues BWE-Papier erschienen
Es ist eine Gretchenfrage in der Windenergienutzung: Was machen wir mit ausgemusterten Rotorblättern? Die Entsorgung und das Recycling der riesigen Bauteile aus Verbundstoffen stellen noch immer eine problematische Aufgabe dar. In einem aktualisierten Papier des Bundesverbandes Windenergie (BWE) zu Rückbau und Recycling von Windenergieanlagen räumt der Verband ein, dass die Verwertung von Verbundmaterialien der Rotorblätter weiterhin eine Herausforderung dar. Glasfaserverstärkte Kunststoffe aus Rotorblätterkönnten derzeit thermisch verwertet, also verbrannt, werden oder als Silikatsubstitut in der Zementindustrie Verwendung finden. Die Verwertung von karbonfaserverstärkten Kunststoffen ist hingegen problematischer – nur wenige Unternehmen befassen sich damit, weitere Forschung sei nötig, schreibt der BWE.
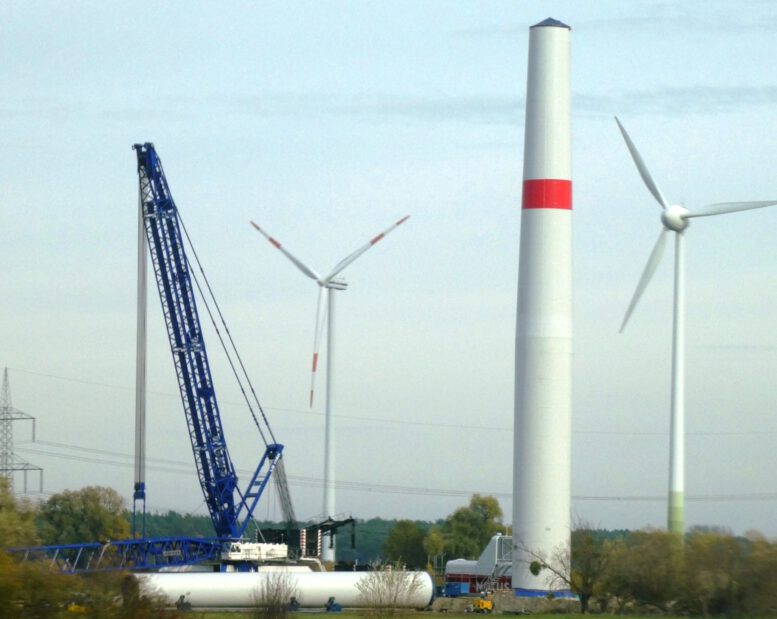
(Rückb-)Bau eines Windgenerators i. d. Lausitz – Foto © Gerhard Hofmann, Agentur Zukunft, für Solarify
Das angeblich mangelhafte Recycling von Windenergieanlagen (WEA) wird immer häufiger als Argument gegen den Ausbau der Windenergie in Stellung gebracht. Dabei wird auf vermeintlich schädliche Umweltauswirkungen bei der Herstellung und Ressourcenverwendung abgestellt. Mittlerweile sind jedoch zwischen 80 und 90 Prozent der Gesamtmasse einer WEA in etablierten Recyclingkreisläufen verwertbar. Mit Bestandteilen aus Stahl und anderen Metallen werden sogar Primärrohstoffe eingespart und weniger Energie für die Aufbereitung als die Neuherstellung verwendet.
Die gesamte Branche ist sich der Verantwortung bewusst und nimmt diese wahr. Bei der Verwertung von Rotorblättern gibt es die größte Herausforderung, da hier oft nur eine thermische Verwertung in Frage kommt. Die Hersteller arbeiten allesamt an komplett recyclingfähigen Lösungen für die Zukunft. Für bereits verbaute Rotorblätter bestehen verschiedene Forschungsvorhaben, um eine echte Weiterverwendung verbauter Bestandteile zu erreichen. Auch wenn durch die Windenergie an Land bei weitem nicht die meisten Abfälle im Bereich der glasfaser- und kohlenstoffverstärkten Kunststoffe produziert werden, wird hier an einer Verbesserung der Entsorgungssituation gearbeitet.
Internationale oder mindestens europäische Standards für das Recycling können helfen, ein einheitliches Vorgehen zu stärken. Dabei ist es besonders wichtig, nicht auf einseitige nationale Regeln zu setzen, da diese spezifischen Anforderungen für den deutschen Markt verursachen würden und somit weiteren Aufwand für die Hersteller bedeuten würden. Europäische Rahmensetzungen sind hingegen geeignet, eine stärkere Berücksichtigung des Recyclingaspekts in allen Mitgliedsstaaten zu stärken. Für die Hersteller würde damit ein einheitlicher Markt gesichert, auf dem sich Skaleneffekte stärker realisieren lassen.
Das vorliegende Informationspapier bildet den aktuellen Stand der Technik ab und verweist auf Forschungsvorhaben und Wege zur Verbesserung des Recyclings insgesamt.
Eine moderne WEA besteht aus vielen Bestandteilen, welche sich hauptsächlich in mineralische und metallische Komponenten sowie in verschiedene Kunststoffarten unterteilen lassen. Größtenteils setzt sich das Gewicht einer markttypischen Anlage wie folgt zusammen:
- Anlagen mit Betonturm zu ca. 80 bis 90 Prozent aus Beton2 (Turm und Fundament)
- Anlagen mit Stahlturm zu ca. 20 bis 25 Prozent aus Beton (Fundament)
Insgesamt spielen Stahlkomponenten mit 30 bis 35 Prozent Gewichtsanteil eine weitere wichtige Rolle bei der Anlagenkonstruktion. Neben der Verwendung im Stahlbeton im Turm findet sich das Material z.B. in der sog. Nabe, an welcher die Rotorblätter befestigt sind und im Maschinenhaus, in dem der Triebstrang mit Rotorwelle, Generator sowie ggf. das Getriebe untergebracht sind. Bei getriebelosen Anlagenkonstruktionen ist kein Getriebe verbaut, der Generator jedoch deutlich größer.
Die Rotorblätter selbst sind in der Regel aus modernen Faserverbundstoffen gefertigt, die regelmäßig auch in Flugzeugen, Zügen oder Autos verbaut werden. Zudem werden Boote aus glasfaserverstärkten Kunststoffen (GFK) hergestellt.
Besonders zwei Verbundstoffarten finden in WEA Verwendung: GFK sowie in deutlich geringerem Maße kohlenstofffaserverstärkte Kunststoffe (CFK). Bei der Produktion werden die einzelnen Fasern (Glas- oder Kohlenstofffaser) in eine sog. Matrix, in der Regel aus duroplastischen Kunststoffharzen wie z.B. Epoxid-, Polyester-, Vinylester- oder einem Polyurethanharz, eingebettet. Die Blattschale selbst ist zudem in sog. Sandwichbauweise konstruiert. Ähnlich einer Fachwerkkonstruktion garantiert die Sandwichbauweise bei geringem Gewicht eine gleichzeitig hohe Steifigkeit. Solche Sandwichmaterialen können Balsaholz oder Kunststoffschäume aus beispielsweise Polyvinylchlorid (PVC) sein. Seit kurzem sind recycelte PET-Sandwichmaterialien verfügbar, die jedoch bei den aktuell zu entsorgenden Anlagen keine Rolle spielen.
Kabelstränge, elektrische Leitungen aus Kupfer, Verkleidungen aus Aluminium oder Gfk stellen einen nur geringen Anteil am Gesamtgewicht einer WEA dar, sind aber im Recyclingprozess wegen ihrer hohen Rohstoffwertigkeit von Bedeutung. Darüber hinaus werden weitere Kupferbauteile im Generator, Transformator und Umrichter verbaut.
In nur geringem Anteil findet sich PVC in einer WEA. Anwendung findet es als Grundstoff für Rohre, als Isoliermaterial für Elektrokabel oder auch im „Sandwich-Kern“ der Rotorblätter in Form von PVC-Schaum.
Zuletzt kommt den Betriebsflüssigkeiten eine wichtige Funktion zu. Hier sind vor allem Öle und Schmierstoffe sowie Hydraulikflüssigkeiten zu nennen, welche den reibungslosen Ablauf der Anlage garantieren und im Rahmen des Rückbaus sachgerecht entsorgt werden müssen. In geringen Mengen sind bei einigen wenigen Anlagen auch glycolhaltige Flüssigkeiten im Kühlkreislauf der Betriebsaggregate enthalten.
Der Rückbau einer WEA läuft in mehreren Einzelschritten ab. Die Rotorblätter werden an der Baustelle unter Schutzmaßnahmen (temporäre Einhausungen und Filtermatten auf dem Boden, Wassernebel) in Einzelteile zersägt und zur weiteren Verwertung abtransportiert.
Das danach folgende Runterbrechen des Turms, sofern es sich um einen Betonturm handelt, erfolgt mit in der Abbruchbranche vorhandenen Geräten und muss sich an den örtlichen Gegebenheiten orientieren. Bei einigen WEA ist das Zerteilen des Anlagenturms in Ringsegmente möglich, die mittels eines Krans heruntergehoben werden. Voraussetzung hierfür ist eine freiliegende, nicht vergossene Abspannung der Segmente. Hierzu sind die Demontagehinweise der Hersteller zu berücksichtigen.
Ein Betonturm kann mittels Abrissbirne oder Abbruchschere abgebrochen werden, die eine effiziente und präzise Bearbeitung des Turms ermöglichen. Das Fallsprengen der Betontürme hat sich als weitere Möglichkeit beim Rückbau etabliert. Voraussetzung sind im Vorfeld durchgeführte Erschütterungsgutachten, wenn Schutzgüter (z.B. Gebäude) in der Nähe der Abbruchstelle vorkommen. Bei der Fallsprengung wird ein Keil in den Betonsockel gesprengt, um den Turm kontrolliert zu Fall zu bringen. Die Möglichkeit der Vollsprengung (Zusammenstürzten des Turms an Ort und Stelle) führt dagegen zu einer deutlich höheren Staubbelastung und wird deshalb nur sehr selten eingesetzt bzw. aus diesen Gründen überhaupt genehmigt.
Das nach dem eigentlichen Abriss freigelegte Fundament wird in der Regel durch einen Hydraulikmeißel in Einzelteile zerlegt. Unter Umständen vorhandene Pfahlgründung aus Betonrammpfählen oder gar Schüttpfählen würden bei Ihrer Entfernung zu unverhältnismäßiger Störung der Bodenstruktur führen und verbleibt daher in der Regel in den tiefen Bodenschichten. Teilweise kommt auch die Lockerungssprengung, besonders bei Fundamenttiefen von mehr als zwei Metern, als sinnvolle Option zum Einsatz.
Zur Zerlegung der Blätter sind Diamantseil- oder Kreissägen, Wasserstrahlschneider oder hydraulische Scheren geeignet. Die anfallenden GFK-Stäube und -Schlämme werden aufgefangen, in dem z.B. Filterfließe unter den Arbeitsbereichen im Vorfeld verlegt wurden und Wassernebel beim Zerteilen eingesetzt wird. Abgeschlossen wird der Rückbauprozess durch das Abtransportieren der zurückgebauten Bestandteile und der Renaturierung der umliegenden Fläche.
Einem abgeschlossenen Rückbauprozess schließt sich die Frage der Verwertung der jeweiligen Stoffe an. Im Allgemeinen werden fast 90 Prozent der zurückgebauten Bestandteile einer WEA, bezogen auf die Gesamtmasse, einem geordneten Verwertungsprozess zugeführt. Im Groben wird zwischen Zweitnutzung, stofflicher und thermischer Verwertung und der Deponierung unterschieden. Die nachfolgenden Punkte informieren über die jeweilige Verwertung der einzelnen Stoffgruppen.
In der zweiten und dritten Betriebsdekade der WEA wird es häufig schwieriger, Originalersatzteile zu bekommen (z.B. Rotorblätter). Da jedoch im Zuge von Repowering-Maßnahmen häufig noch gut erhaltene Gebrauchtteile vorhanden sind, können diese bei WEA ab der zweiten Betriebsdekade nach Prüfung und ggf. Überarbeitung weiterverwendet werden. In diesem Second-Hand-Markt werden ca. 10 Prozent der Komponenten der abgebauten WEA einer Zweitnutzung zugeführt.
Der im Rahmen des Rückbaus anfallende Betonaufbruch kann nach Bedarf direkt vor Ort aufgearbeitet bzw. recycelt werden. Dazu wird der Betonabbruch durch Brecher zu Betonsplitt oder Betonschutt zerkleinert und kann regional für den Wege- oder Fundamentbau weiterverwendet werden. Alternativ wird Betonschutt als Rohstoff für Recyclingbetone eingesetzt.
Spezielle Anforderungen an das Recycling der WEA gibt es nicht, sodass die im Verhältnis zur Baubranche sehr geringe Mengen an anfallenden Betonschutt von den seit Jahrzehnten etablierten Prozessen und Recyclingstrukturen ohne Weiteres aufgenommen werden können.
Wenn die elektronischen Bestandteile nicht mehr auf einem Second-Hand-Markt verkauft werden können, bietet sich eine stoffliche Verwertung der in der Elektronik vorhandenen Kunststoffe und Metalle (u.a. Gold, Platin) an. Dazu müssen die Bauteile zuerst von Hand demontiert werden, bevor sie einen Schredder durchlaufen. Die anschließend separierten Metalle können dem Markt zurückgeführt werden. Für die verbliebenen Kunststoffe bietet sich die thermische Verwertung, zum Beispiel zur Strom- oder Wärmegewinnung in speziellen Müllverbrennungsanlagen, an.
Bei elektronischem Schrott (z.B. Leiterplatinen, Umrichter, Kondensatoren) fallen des Weiteren seltene Erden und Edelmetalle an, welche einer besonderen Behandlung bedürfen.
Der im Zuge des Rückbaus anfallende Stahlschrott ist ein hochwertiger Rohstoff, der auf dem Sekundärrohstoffmarkt weiterverkauft wird. Wichtig hierbei ist die exakte Trennung der Metalle in Eisen- und Nichteisenmetalle. Eingeschmolzene Metalle lassen sich problemlos zu neuen Bestandteilen formen. Das Recycling von Stahlbestandteilen stellt so einen wichtigen Beitrag zur Sicherung der Stahlproduktion in Deutschland dar, da diese nicht vollständig durch Primärrohstoffe zu decken ist. Das hat den Vorteil, dass deutlich weniger Energie als bei der Herstellung von Stahl aus Eisenerz benötigt wird.
Ausgediente Kupferteile werden vom Metallhandel erfasst, aufgearbeitet und anschließend an Kupferhütten zum Einschmelzen weiterverkauft. Recycelte Kupferbestandteile haben auch nach mehrmaligem Recycling die gleichen Eigenschaften wie Primärrohstoffe. In Deutschland hat sich das Kupferrecycling seit Langem etabliert; die Recyclingquote liegt hier bei über 45 Prozent.8 Dadurch wird eine Ablagerung auf Deponien weitestgehend vermieden und Primärstoffe werden eingespart.
Nach dem Entfernen der Aluminiumteile von groben Verunreinigungen werden diese in Öfen, zusammen mit Zusätzen, bei hohen Temperaturen und unter ständiger Bewegung des Ofeninhaltes eingeschmolzen.
Bisher wird die Gesamtheit des anfallenden Aluminiums, auch aus anderen Branchen, sehr selten legierungsrein sortiert und recycelt. Neue Prozesse und Techniken machen dies jedoch mittlerweile möglich und unterstützen so ein höherwertigeres Aluminiumrecycling. Dadurch kann das recycelte Aluminium als Rohstoff für mehr als nur Druckgussaluminium dienen.
Das Recycling von Aluminium hat den Vorteil, dass dabei weniger als ein Zehntel der Energie, die zur Herstellung von primärem Aluminium aus Bauxit benötigt ist, verbraucht wird.
Die Verwertung von PVC hat sich seit vielen Jahren etabliert. Größtenteils wird es zusammen mit anderen Kunststoffen verbrannt und zur Energiegewinnung oder der Erzeugung von Synthesegasen genutzt. Die in den Verbrennungsöfen eingebauten Filter filtern zuverlässig die Chloride aus PVC-armen Abfällen und neutralisieren diese.
Bei PVC-reichen Abfällen können in speziellen Anlagen die Chlorwasserstoffe auch separat abgeleitet und zur Wiederverwendung in der Neuproduktion von PVC verwendet werden. Dafür müssen diese PVC-reichen Teile (z.B. Rohre aus der Elektroinstallation) aus den WEA sortenrein dem Recycling zugeführt werden.
Zu den Betriebsflüssigkeiten gehören besonders die in der Anlage verwendeten Öle. Bei diesen handelt es sich um Betriebsstoffe, die selbstverständlich nicht in die Umwelt gelangen sollten, weswegen die Separierung der Öle von geschultem Fachpersonal unter Zuhilfenahme spezieller Maschinen, die auch im Wartungsprozess beim Ölwechsel der Anlagen verwendet werden, abgesaugt und abtransportiert werden.
Aus gebrauchtem Altöl lässt sich durch erneutes Raffinieren und Aufarbeiten hochwertiges Basis-Öl gewinnen, das in Punkto Viskosität und Schmiereigenschaften neuem Öl in keiner Weise nachsteht. Altölrecycling leistet somit durch Kohlenstoffdioxidreduktion und Ressourcenschonung einen konsequenten Beitrag zum Klimaschutz.9 Die bestehenden und zukünftigen Kapazitäten der Altölwirtschaft stellen auch auf Dauer die umweltgerechte und sichere Entsorgung und das Recyceln der Öle sicher.
Die Verwertung von Verbundmaterialien der Rotorblätter stellt weiterhin eine Herausforderung dar. Insgesamt wurden im Jahr 2015 in Europa 1.069.000 Tonnen GFK produziert. Davon wurden 34 Prozent in der Konstruktions-Branche verbraucht, zu der auch die Windindustrie gehört. Die Bereiche Transport (35 Prozent) sowie Elektronik- und Sportgeräte (30 Prozent) weisen ebenfalls einen sehr hohen GFK-Verbrauch auf. Dagegen entfallen bei CFK nur etwa 14 Prozent des Verbrauchs auf die Windindustrie. Die größten Abnehmer sind die Luftfahrtindustrie, das Militär (zusammen 31 Prozent) sowie die Fahrzeugindustrie (21 Prozent).
Die im Zuge des Rückbaus anfallenden ausgedienten Verbundstoffe können auf unterschiedlichste Art verwertet werden. In der Vergangenheit wurden Faserverbundteile wie GFK auf Deponien entsorgt. Mit der Änderung der Abfallablagerungsverordnung (AbfAblV) und Deponieverordnung (DepoV) ist dies jedoch seit 2005 auf Grund der speziellen Zusammensetzung und des hohen thermischen Energiegehaltes nicht mehr gestattet.
Glasfaserverstärkte Kunststoffe sind mitnichten wertloser Abfall, der keine sinnvolle Verwertung finden kann. Da die GFK ca. je zur Hälfte aus Fasern und Harzen bestehen, können 50 Prozent des Materials (Kohlenwasserstoffe der Harze) in etablierten Verfahren thermisch verwertet und die Energie zur Wärmegewinnung genutzt werden. Allerdings können klassische Müllverbrennungsanlagen Verbundwerkstoffe nur bedingt in größeren Mengen mitverbrennen.
Die restlichen 50 Prozent der übrigbleibenden Glasasche wird als Silikatsubstitut in der Zementindustrie einer stofflichen Verwertung zugeführt. Dazu werden die zerkleinerten Rotorblätter z.B. in das in Bremen ansässige und mit dem GreenTech-Award ausgezeichnete Unternehmen „neocomp GmbH“ gebracht. Nach der Anlieferung werden die Rotorblätterbestandteile dort gewogen und einer Annahmekontrolle unterzogen. Leistungsstarke Schredder zerkleinern daraufhin die Rotorblattteile in mehreren Schritten auf Kantenlängen von ca. 50 mm und sortierten metallhaltige Materialien (z.B. Blitzableiter des Blatts) aus, die dem Metallrecycling zugeführt werden.
Die restlichen brennbaren Bestandteile des ursprünglichen Rotorblattes werden anschließend zusammen mit anderen Abfallresten und Zusatzstoffen (z.B. Papier) als Ersatzbrennstoff in der energieintensiven Zementindustrie thermisch verwertet und ersetzen so fossile Energieträger wie Kohle oder Gas. Die z.B. im Zementwerk Lägerdorf der Holcim GmbH südlich von Itzehoe anfallende Asche dient dann als Rohsandersatz im Zement, der wiederum z.B. im Fundament neuer WEA verbaut werden kann. 11 Aktuell werden in der Zerkleinerungsanlage der neocomp GmbH in Bremen ca. 30.000 Tonnen pro Jahr verarbeitet, was einen entscheidenden Beitrag zur Materialentsorgung darstellt.12 Die Anlage kann jährlich bis zu 120.000 Tonnen Alt-GFK zerkleinern, sodass Kapazitätsengpässe nicht abzusehen sind.
Diese Form der thermischen und stofflichen Verwertung ist zurzeit die sinnvollste Art, anfallende GFK-Abfälle aus allen Industriebereichen nach ihrem Gebrauch zu verwerten. Da derzeit in der Forschung weitere innovative Recyclingtechniken ausgelotet werden, wird es in Zukunft auch neue, noch nachhaltigere Methoden auf dem Markt geben. Beispielsweise werden bereits Dachelemente aus recyceltem GFK am Markt angeboten.
Eine thermische Verwertung von CFK-Bestandteilen (ähnlich wie bei GFK) ist eine naheliegende Option, gilt aber als problematischer, da Kohlenstofffasern Strom leiten und so bei den oft eingesetzten elektrostatischen Filtern der Müllverbrennungsanlagen zu Defekten führen können. Neue Filtertechnologien sind hier gefragt und befinden sich aktuell in der Entwicklung. Ideen für eine bessere thermische Verwertung sind aktuell Gegenstand eines Forschungsprojektes der RWTH Aachen. Dort hat man das bisher genutzte und etablierte Verfahren der Pyrolyse verfeinert, wobei das CFK unter Sauerstoffabschluss auf bis zu 1500°C erhitzt und mit Kohlendioxid und Wasserdampf in Kontakt gebracht wird, sodass störende Rußablagerungen vermieden und die Qualität des Recyclingmaterials verbessert werden kann. Auch gibt es für CFK-Bestandteile schon die Möglichkeit eines „Faser-zu-Faser-Recyclings“ der Kohlenstofffaser, wie es bereits seit Jahrzehnten beim Altpapier oder Altglas in Deutschland angewendet wird.
Zwei der Firmen, die sich auf ein solches Verfahren spezialisiert haben, sind beispielsweise CFK Valley Stade Recycling GmbH & Co. KG und CarboNXT GmbH. Im ersten Schritt werden die abgetrennten CFK-Teile der WEA nach Niedersachsen zu CFK Valley Stade Recycling GmbH & Co. KG geliefert, um dort weiterbearbeitet zu werden. Hauptaufgabe ist es, die Carbon-Fasern von der Matrix zu lösen und zu separieren. Dies kann mittels chemischer (Solvolyse), thermischer (Pyrolyse) oder enzymatischer Verfahren geschehen. Jedoch wird bis dato in erster Linie das thermische Zersetzungsverfahren umgesetzt. Dabei werden die zerkleinerten Rotorblattbestandteile unter Ausschluss von Sauerstoff auf mindestens 500°C in einer speziellen Anlage erhitzt. Dadurch werden die langkettigen organischen Kohlenstoffverbindungen der Harze aufgebrochen, als Gase abgeführt und verbrannt. Übrig bleiben die Fasern in ihrer ursprünglichen Form. Diese freigelegten Faserteile können nach diesem Prozess kundenindividuell veredelt und z.B. zu sog. Carbon-Pellets weiterverarbeitet werden. Diese können anschließend Verwendung in neuen Produkten, zum Teil in der Autoindustrie oder im Maschinenbau, finden. Auch in der innovativen 3D-Drucktechnologie können rezyklierte Carbon-Filamente eingesetzt werden und damit neue Fasern ersetzen.
In der Zukunft wird es darauf ankommen, weiter Forschung zu betreiben, die vorhandenen Kapazitäten auszubauen und Vorbehalte gegenüber recycelten Materialen als Rohstoffe der Industrie abzubauen.
Wie in Kapitel 1 dargestellt, sind vom Gewicht einer WEA ausgehend ungefähr 80 bis 90 Prozent der eingesetzten Materialien wiederverwendbar. Für die übrigen Bestandteile wird es in Zukunft innovative und wirtschaftliche Verwertungsmöglichkeiten geben. Voraussetzung ist dazu auch, dass in Forschung und Entwicklung investiert wird, um die vorhandenen Ideen (z.B. Pyrolyse, Solvolyse) zu verbessern und markttauglicher zu machen.
Der europäische Windverband WindEurope gibt in einer gemeinsamen Studie mit dem europäischen Chemieverband (The European Chemical Industry Council) und dem europäischen Verband der Verbundwerkstoffe (European Composites Association) einen Überblick („Umrisse der besten Strategien für das Recycling von Windturbinenblättern“) zu aktuellen Recyclingstandards, der zu erwartenden Anzahl demontierter Blätter, zu laufenden Forschungsprojekten und aktuellen gesetzlichen Regelungen/Vorgaben in den EU-Mitgliedstaaten. Darüber hinaus werden Empfehlungen zu Forschung und Entwicklung sowie das zukünftige Design für ein verbessertes Recycling von Verbundmaterialien ausgesprochen16.
Einige Forschungsprojekte beschäftigen sich zurzeit in Deutschland mit Recyclingfragen:
- Das Projekt „WEAcycle“ (Entwicklung eines Konzepts und Maßnahmen für einen ressourcensicheren Rückbau von WEA) wurde 2017 durch das Bundesumweltamt gestartet. Es gliedert sich in fünf Arbeitspakete und wurde von dem dänischen Consultingunternehmen Ramboll BBB, sowie dem Institut für Aufarbeitung und Recycling der RWTH Aachen begleitet. Das erste Arbeitspaket beschäftigte sich mit den Rahmenbedingungen für den Rückbau und das Recycling, um die rechtlichen Vorgaben, derzeitige technische Praxis und umweltfachliche Bewertung aufzuzeigen. Das zweite Arbeitspaket widmete sich der Erstellung von Abfall- und Rückbauprognosen bis zum Jahr 2040, auf Grundlage unterschiedlicher Datensätze. In den folgenden Arbeitspaketen wurden, aufbauend auf den Ergebnissen der vorherigen Kapitel, Empfehlungen für den Rückbau und das Recycling ausgearbeitet. Auch an Ratschlägen für die organisatorische und finanzielle Umsetzung von Rückbauvorhaben wurde gewirkt. Das Projekt wurde Ende Mai 2019 abgeschlossen und die Ergebnisse im November 2019 veröffentlicht.
- Das Forschungsvorhaben „Verwertungsnetzwerk RecycleWind – resilient und selbstlernend“ der Hochschule Bremen in Zusammenarbeit mit der Beratungsfirma brands & values GmbH beschäftigt sich mit einem Verwertungsnetzwerk. Ziel ist es, ein selbstlernendes Netzwerk mit den wichtigsten Akteuren (beteiligte Firmen und Behörden) für alle Stufen einer WEA zu etablieren, um eine ressourcenschonende Lenkung von Stoffströmen festlegen zu können.
- Gemeinsam mit PartnerInnen aus Wissenschaft und Industrie haben ForscherInnen des Instituts für Leichtbau und Kunststofftechnik (ILK) der TU Dresden im FOREL-Technologieprojekt ReLei unter der Projektleitung der ElringKlinger AG einen Technologiedemonstrator entwickelt, an dem das Thema Recycling konsequent umgesetzt wurde. Schon bei der Bauteilkonzeption und -auslegung berücksichtigte das Projektteam den Einsatz von recycelten Kohlenstofffasern und wiederaufbereitetem Spritzgießgranulat. „Das Forschungs- und Entwicklungsvorhaben ReLei wird mit Mitteln des Bundesministeriums für Bildung und Forschung (BMBF) im Rahmenkonzept „Innovationen für die Produktion, Dienstleistung und Arbeit von morgen“ mit Mitteln aus dem Energie- und Klimafonds gefördert (Förderkennzeichen 02PJ2800 – 02PJ2808) und vom Projektträger Karlsruhe (PTKA) betreut. ReLei wurde 2015 vom BMBF als Leuchtturmprojekt ausgezeichnet.“
- Das Forschungs- und Entwicklungsprojekt der TU Bergakademie Freiberg wird mit Mitteln des Bundesministeriums für Bildung und Forschung (BMBF) im Rahmenkonzept „Forschung für die Produktion von morgen“ (Förderkennzeichen 02P16Z014) und mit Mitteln aus dem Energie- und Klimafonds gefördert und vom Projektträger Karlsruhe (PTKA) betreut.
Der BWE sieht insbesondere folgende Herausforderungen:
I. Bisher wurden verhältnismäßig wenige Anlagen zurückgebaut. Ein Teil dieser Anlagen wurde auf dem Zweitmarkt, zumeist außerhalb der EU, umgesetzt. Die in Recyclingkreisläufe rückzuführenden Stoffmengen sind deshalb bisher sehr überschaubar. Dadurch konnten sich noch keine allgemein gültigen Verfahren oder Standards etablieren. Es gibt eine Vielzahl von Unternehmen, die sich mit dem Rückbau von WEA befassen und dafür in Abstimmung mit den unteren Abfallbehörden eigene Regeln erarbeitet haben.
II. Um einen guten Verwertungsprozess zu ermöglichen, sind detaillierte Informationen über die Materialzusammensetzung der WEA erforderlich. Da ein Teil der Hersteller inzwischen nicht mehr am Markt ist, gestaltet sich dies für den bestehenden Anlagenpark schwierig.
III. Die Verwertung und Entsorgung der Glas- und Kohlefaserteile der Rotorblätter und Gondelverkleidungen wurden bereits in der Bund/Länder-Arbeitsgemeinschaft Abfall (LAGA) eingehend erörtert. Die Empfehlungen hinsichtlich Abfallschlüssel und Kennzeichnungsempfehlungen für faserhaltige Abfälle in Kunststoffmatrix (GFK und CFK) gilt es umzusetzen.
IV. Die Nachfrage nach sekundären Rohstoffen ist aktuell zu gering und von Vorbehalten auch durch die Qualitätsverluste des recycelten Materials geprägt. Um recycelte Materialien gezielt in neuen Produktgruppen einzusetzen, braucht es eine Informationsoffensive, die ähnlich wie bei der Verwendung von Recyclingpapier für eine breite Akzeptanz sorgt.
Der Bundesverband Windenergie e.V. unterstützt die Bestrebungen der Branche, einen geordneten Rückbau und eine sinnvolle Verwertung zurückgebauter WEA zu sichern. Dazu begleitet der Verband verschiedene Projekte der Branche und Behörden und fordert alle Akteure auf, gemeinsam globale bzw. mindestens europäische und einheitliche Regeln zu erarbeiten. Der BWE spricht sich ausdrücklich für einen europäischen Standard aus. In der Vergangenheit wurden für die Windbranche zahlreiche unterschiedliche nationale Standards und Vorschriften geprägt. Dies betrifft unter anderem Sicherheitsmarkierungen an Anlagen, Vorgaben für die Luftfahrt, baurechtliche Vorschriften, Vorgaben für den Einsatz von Servicepersonal, etc. Um die Industrialisierung der Windindustrie zu unterstützen, macht es Sinn, möglichst viele international gültige Vorschriften und Standards zu nutzen. Einheitliche Standards führen in der Regel zu Effizienz in der Herstellung und im internationalen Handel, auch können sich gesetzliche Vorgaben in einzelnen Ländern auf internationale Rahmenvorgaben / Best Practice-Beispiele beziehen. Wenn Standards auf internationaler Ebene erstellt werden, werden außerdem zahlreiche Sichtweisen, Best Practice-Fälle und Meinungen verschiedener ExpertInnen berücksichtigt. Wichtig ist darüber hinaus ein breiter Konsens innerhalb der Branche. Dieser ist einer rein nationalen Lösung deutlich vorzuziehen. Daher wird parallel zu den deutschen Überlegungen auch die Arbeit an einem einheitlichen Standard auf europäischer Ebene bei WindEurope und der dort installierten Working Group Sustainability / Task Force Decommissioning unterstützt.
Aus Sicht des BWE sind folgende Herausforderungen zu beantworten:
I. Ein einheitlicher Rückbaustandard
- Ein einheitlicher Rückbaustandard wird als gute fachliche Praxis etabliert.
- WEA sind dabei in ihrer Gesamtheit, inkl. Fundament vollständig zurückzubauen. In einigen Regionen sind die obersten Bodenschichten sehr weich, nachgiebig oder feucht. Hier reicht ein Flachfundament oft nicht aus. Deshalb wird dann auf eine Pfahlgründung zurückgegriffen, um die nicht tragfähigen Bodenschichten zu überbrücken und dafür zu sorgen, dass die Baulast tief in der Erde auf einem stabilen Untergrund abgetragen werden kann bzw. über die Reibungsfläche der Pfähle die Last in den Untergrund abgeleitet werden kann. Diese Pfahlgründungen reichen daher weit in die Tiefe und durchstoßen unter Umständen wasserführende Schichten. Beim Rückbau sind diese Fundamente bis oberhalb der Pfahlgründung zu entfernen, da die komplette Entfernung unverhältnismäßige Störungen der Bodenstruktur nach sich ziehen würde.
- Die im Rahmen des Rückbaus erforderliche Zerlegung von Komponenten soll weitgehend vor Ort umgesetzt werden.
- Um Staubemissionen zu vermeiden, muss die Vorzerkleinerung insbesondere der Rotorblätter unter Abschirmung erfolgen.
- Insgesamt ist die Diffusion in den Boden durch geeignete Abschirmungen, den Einsatz von Wassernebel und/oder Filtermatten unterhalb der Zerlegungsflächen zu vermeiden.
- Lärmemissionen müssen auch bei Abbrucharbeiten die gesetzlichen Grenzwerte unterschreiten.
II. Eine vereinfachte und geordnete Verwertung der zurückgebauten Materialien
- Die Einführung eines Abfallschlüssels für CFK und GFK in der Abfallverzeichnis-Verordnung ist erforderlich. Ein Abgleich mit internationalen, mindestens aber europäischen Normen muss erfolgen.
- Um die Verwertung zu vereinfachen, müssen die Hersteller zukünftig für alle wesentlichen Komponenten der WEA einheitlich strukturierte Datenblätter vorliegen, die ausreichende Informationen über die eingesetzten Rohstoffe, Bauteilmaterialien und -mengen liefern.
- Der Einsatz gebrauchter Rotorblätter im Inland bleibt möglich. Der Export von gebrauchten Rotorblättern, die älter als fünf Jahre sind, soll nur dann möglich sein, wenn ein Einsatz nachgewiesen wird.
- Die Entsorgungsnachweise sind regelmäßig den unteren Abfallbehörden vorzulegen und werden dort archiviert.
- Der Rückbau und Recyclingprozess sollten in allen Mitgliedsstaaten der Europäischen Union nach einem gleichen Standard erfolgen.
->Quellen:
- erneuerbareenergien.de/patent-aus-der-schweiz-altes-rotorblatt-traegt-pv-anlage
- wind-energie.de/09-rueckbau/20230801_BWE-Informationspapier_Rueckbau_und_Recycling_von_Windenergieanlagen.pdf
- erneuerbareenergien.de/patent-aus-der-schweiz-altes-rotorblatt-traegt-pv-anlage
- wind-energie.de/BWE-Informationspapier_Rueckbau_und_Recycling_von_Windenergieanlagen.pdf